A Passion for Learning
We are open to new ideas. And we want to establish a new way of learning that is designed to prepare GF for a changing world of work. Together with her team, Nesibe Bruggmann is aiming to make this philosophy an integral part of the company.
Nesibe is passionate about learning – and this passion is what brought her to GF over five years ago. She interviewed with the company in the spring of 2016 for a Talent Management & Learning internship in the Corporate HR team in Schaffhausen (Switzerland). “During the interview, I said I wanted to keep learning and improving every day,” she recalls as if it were yesterday. “I know now that sentence was the reason I was offered the position.”
Nesibe is true to her word. She established herself in the company and expanded her horizons. “During my internship, I learned about all the types of training offered by the GF Academy – cross-divisional training courses at the corporate level – and helped set some of them up,” she says. “That’s when I knew I wanted to keep working in this area for a long time to come.” After finishing her internship in the Corporate HR team, Nesibe moved to the GF Machining Solutions division, where she was responsible for improving global HR processes and implementing the Me@GF platform as an HR Specialist. At the beginning of 2020, she received an offer from Schaffhausen that she could not refuse. Since then, she has served as Head of Learning and Development, overseeing the ongoing development of the culture of learning at GF and global training measures at the corporate level. Part of her role is creating a new, global learning platform called MyLearning@ GF.
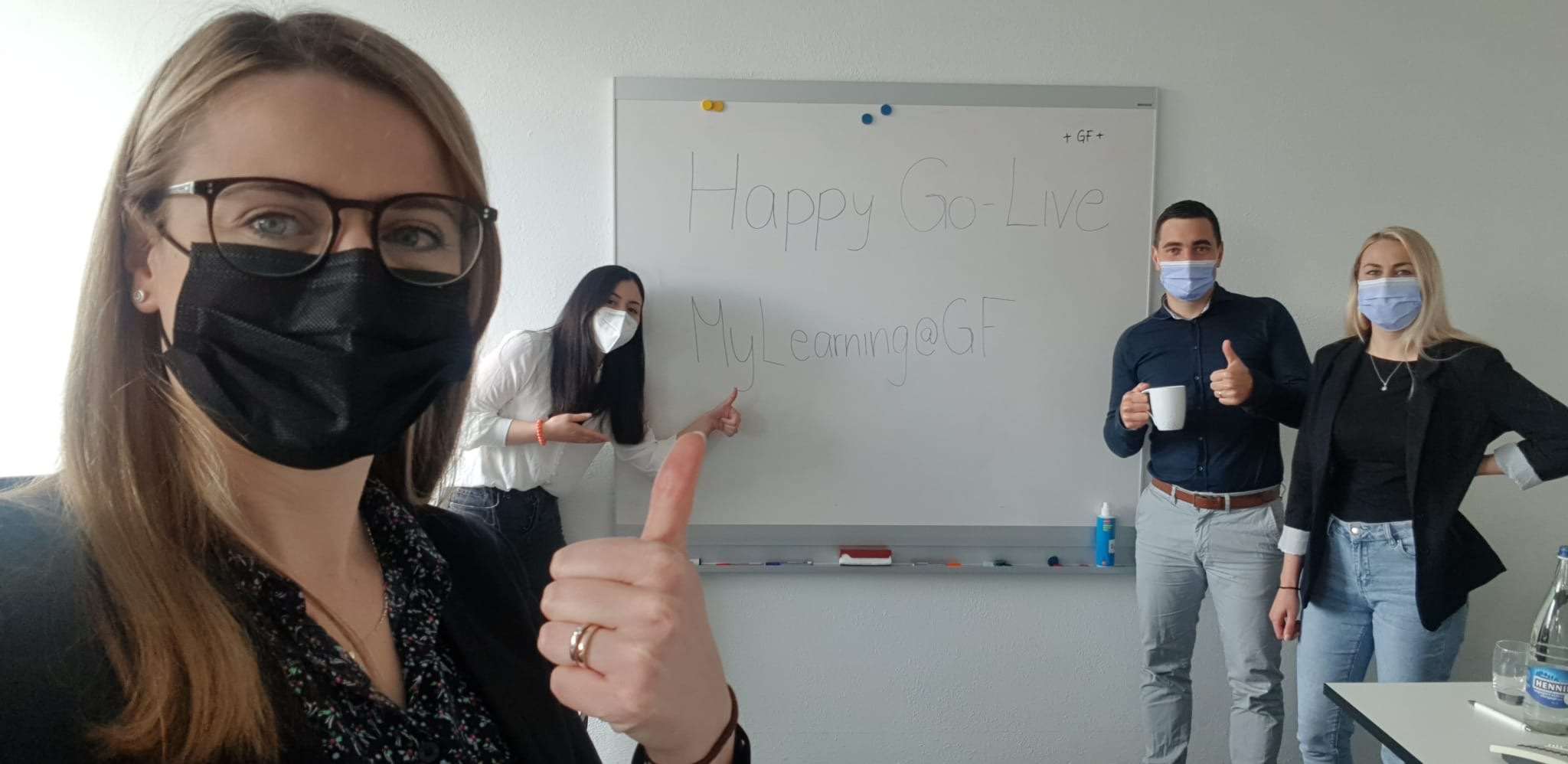
Learning is valuable
Nesibe’s work has become even more important since the beginning of 2021, when the implementation of the GF Strategy 2025 gave new impulse to the culture of learning. GF is aiming to make “Learning” a key part of the corporate culture, along with “Performance” and “Caring.” Nesibe sees this as a logical step: “Our vision is for each and every one of us to make learning part of our everyday routine.” The new MyLearning@GF online learning platform is designed to help employees do just this. It went live with a pilot in May.
“It’s okay to make mistakes – as long as we are quick to learn from them.”
Nesibe Bruggmann, Head of Learning and Development
Why is the company making learning a central pillar of its new target culture now in particular? The GF Piping Systems, GF Casting Solutions, and GF Machining Solutions divisions are already world-class today. But the working environment is undergoing a transformation. “Our world is changing faster – and the markets we currently lead in are changing along with it,” says Nesibe. Digitalization, efforts to boost sustainability, and most recently the coronavirus crisis are pushing old certainties aside and making long-successful business models obsolete. “We have to respond by becoming faster and more agile. We need to be bolder and more confident about taking new approaches.”
More digital, more flexible
The same applies to learning offers at GF, of course. “GF has always had high-quality training offers,” says Nesibe. “Our new learning platform will first and foremost make us more digital and more flexible.” GF employees who visit MyLearning@GF will find new opportunities to develop themselves as employees. New learning content and formats will be continually adapted to the GF strategy and the needs of the teams and employees in order to build up the right skills and stay ahead of the curve. “Going forward, we will be focusing on a mix of digital self-study, online seminars, and in- person events,” Nesibe says.
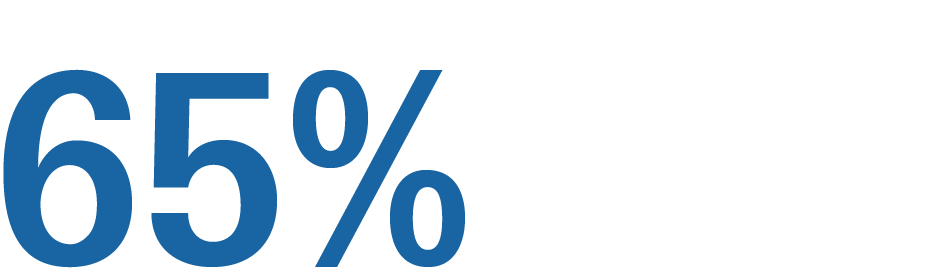
of all children worldwide will choose a profession when they are adults that does not yet exist.
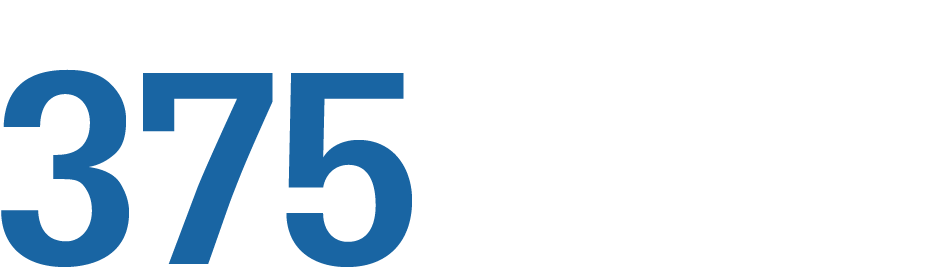
million people worldwide will have to acquire completely new skills or learn a different profession by 2030. This corresponds to 14 percent of all employees.
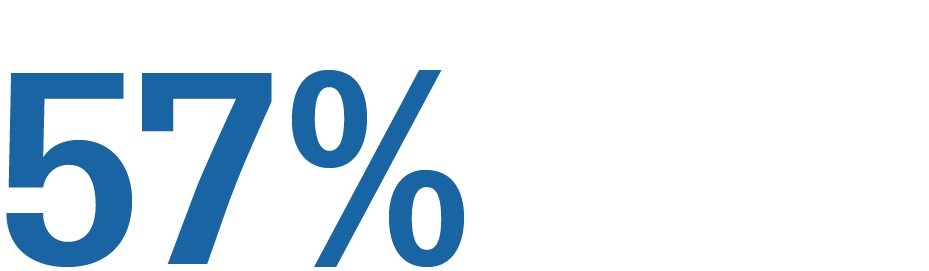
of all managers see soft skills as more important than hard skills. This is because soft skills cannot be replaced by machines.
She and her team are aiming to instill a new way of thinking among employees. Their message: You can learn anytime and anywhere! It does not matter whether it is during daily routines, from experienced colleagues, or bit by bit. “We don’t always have to participate in comprehensive training programs,” Nesibe says. “Every day, each of us should ask ourselves, what can I learn by watching the best members of my team – and how can I make our values an active part of my daily work?”
But Nesibe believes that making a new culture of learning an integral part of GF will take more than modern platforms: “As one of our values, Learning means that we are open to new ideas. In other words, learning isn’t a task that I check off my list once a year,” she says. “Everything that we do is an opportunity to learn something new and to share what we have learned with each other.” Nesibe and her team are already seeing how well this can work in training sessions they have reorganized. “It’s fantastic to see how colleagues from various areas who are meeting each other for the first time can talk openly about mistakes and learn from each other’s expertise,” she enthuses while describing the recent training sessions. “This is what we want to achieve.”
Making mistakes is part of life
But what needs to happen to make this culture of learning from each other part of everyday work at a company that has always been about thinking precisely and the pursuit of technical perfection? It is not always easy for experienced engineers or long-time employees in particular to embrace new things and speak openly about aspects that are not working as well as they could. Nesibe thinks the key is a new awareness about dealing with failure. “It’s okay to make mistakes,” she says, “as long as we are quick to learn from them.”
Of course, there are different types of mistakes. There should not be any mistakes in situations that would have severe consequences – for example, when it comes to safety at work or standardized production processes involving large quantities. But: “Some mistakes can help us learn and can even be useful – for example, when developing prototypes,” says Nesibe.
One prime example could be the startup scene, where you begin by focusing on developing a minimum viable product (MVP) at high speed. The MVP is an initial version of the product with the key basic functions, which is then developed continually by incorporating customer feedback. “We are using this same approach in the development of the MyLearning@GF platform so we can improve the system as well as the spectrum of learning offers on an ongoing basis,” Nesibe says.
New things take time
Nesibe knows it will take some time for the new learning platform to become established throughout GF. “While working at GF Machining Solutions, I came to understand how long it takes for concepts from the corporate area to reach everyone else.” This was why she implemented the project together with colleagues from the three divisions; in all, 16 people were involved worldwide. Nesibe is certain that the advantages offered by the new system will ultimately win over all employees at GF. In the future, the benefits will also include, for example, the option of training customers in the correct use of new machines.
Whether it’s customers or employees, “You can tell when people are getting into the flow and are enthusiastic about the know-how they are acquiring. That’s what we want to achieve with MyLearning@GF, too,” Nesibe says, and her eyes begin to light up. There it is again – the passion for learning.
“We want to encourage people to learn”
Nesibe Bruggmann puts her heart into the topic of learning – and the new learning platform for GF. In this interview, she talks about the development phase, her expectations, and inspiration.
What role does MyLearning@GF have to play for the future culture of learning at GF?
for the future culture of learning at GF? MyLearning@GF is the first central platform at GF that promotes learning from and with each other. The platform’s intuitive interface is designed to encourage employees to engage in regular learning, anytime and anywhere. During a second phase, we want to make the content available to colleagues in production, as well.
What was the biggest thing you learned from the project yourself?
There were a lot of challenges, because part of the team was on short-time work due to the pandemic and we could only collaborate online. So it was all the more important to make sure everyone was always on board and not let setbacks get us down, either. If you put your heart and soul into working toward a shared goal as a team, you’ll be successful.
Where do you get ideas and inspiration for your work?
I speak with people from my personal environment and from GF, of course. Now and then I talk with the colleague who supervised me when I did the internship. She works at a different company now, but we still stay in touch. I also like using social networks like LinkedIn, watching TED Talks, or reading specialist articles.
Three employees share how they are already making learning an active part of their day-to-day work
“The most important thing is addressing mistakes openly and learning from them”
Sebastian Felkl
Identifying disruptions and optimizing work processes are key parts of my job. Making mistakes is human, and nothing we need to be ashamed of. The most important thing is that we learn from them. Speaking openly about things that do not go well is the basis for continuous improvement. One day before the opening ceremony of the new greenfield foundry of GF Linamar in Mills River, I damaged a casting tool because of incorrect machine settings. I immediately talked to the team. With joint efforts, we were able to repair the tool just in time. It felt great for the entire team to present the new machine to our customers and guests the next day. Even if something goes wrong, we can still turn it into something positive, and learn from it. In the future, I will always use the right settings for this machine. Let’s keep on sharing our lessons learnt.
“I challenge myself, give new things a try, and aim to be persistent when learning something new.”
Martha Gil
I challenge myself, give new things a try, and aim to be persistent when learning something new. Identifying a coach who can support you in developing new skills can be very helpful. For my new role as focus factory lead, I had to learn how to build new products and take leadership responsibility for a few team members – a great opportunity! I advanced my skills in lean management in internal training courses and Kaizen events. I also keep learning from own experience. Once I didn’t check the method sheets for a production line I was in charge of. I made a mistake because I assumed I knew how it had to be done since I used to work on this line. Luckily, I was able to correct the mistake and apologized to my team. Better consult colleagues working on the production line first and don’t assume that things do not change.
“The innovation game takes courage, the right people, and the right environment to fail often and succeed sooner!”
Oliver Rosin
I want to improve the ergonomics for operators of GF milling machines. I can implement my idea: connect VR glasses to our machines. Key data now appears in the operator’s field of vision instead of on the machine monitor. For my project, I collaborate with many people and had to present my idea to our top management. This meant stepping out of my comfort zone. Kickbox gave me the right methodology and confidence to do so. A low point was when the remote connection didn’t work as planned. I ran out of ideas and deadlines got tighter. Together with colleagues from IT, we came up with a different approach. It worked! I was able to analyze my mistakes and learnt how to resolve them. What I learnt: The innovation game takes courage, the right people, and the right environment to fail often and succeed sooner!
The KICKBOX Initiative
Kickbox is a Design Thinking initiative that encourages employees to embrace their entrepreneurial nature and create valuable business innovations. Participants of the initiative learn how to collaborate with customers and colleagues to design, test, pitch and bring to market their own idea. Launched as a pilot by GF Machining Solutions in Switzerland in November 2019, Kickbox has already generated more than 50 ideas. The best ones were presented to a jury including top management at the Kickbox Demo Day in November 2020. Three projects including the one of Oliver Rosin are currently being piloted with customers.